Collaboration for quality
09.22.2017
As part of its programme of innovation and continuous improvement, water treatment specialists Marsh Industries has constantly sought to build partnerships with experts and academics to share knowledge, best practice and achieve product excellence.
Marsh Industries has been built on partnerships and collaboration right from the get go when founder and MD Steve Boyer was looking at ways to improve tank quality. “I could never understand why manufacturing with fibreglass in the marine and automotive industry looked sleek whereas in the building sector it could sometimes look less polished,” he says. To that end Marsh worked with an international boat builder based in Northamptonshire and, with their active involvement, adopted some of the techniques they use. For example, using auto spray guns that mix the glass, resin and catalyst solution which results in both consistency of the mixture and very little wastage.
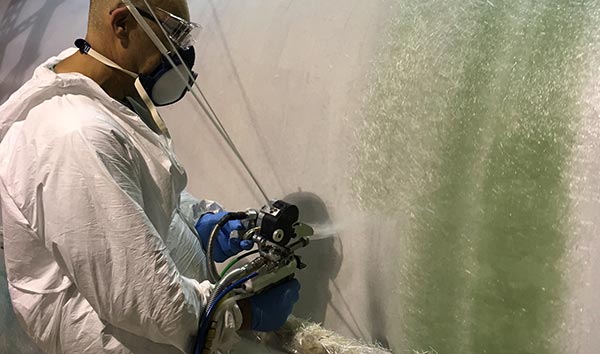
Once that technique had been perfected, Marsh began to collaborate with Loughborough University’s Engineering Department to develop a bespoke design and quotation programme, Gaia Sege© that allows contractors and specifiers to design a system quickly that will not only suit all of their specification and performance requirements, but will also comply with all relevant industry, environmental and legal requirements. “Specifying an off-mains system may not be something that many contractors have to do every day, and designing an efficient and compliant system is a complex business,” says Steve. “This unique system makes the process much simpler. Users can go through a simple click and select process and we will produce a bespoke, professional design and quotation back with all the information you need for a straightforward and cost-effective project.”
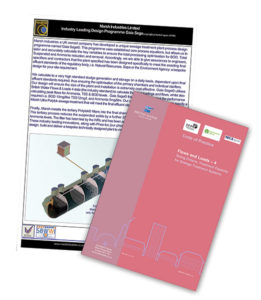
Using key process parameters Gaia Sege will design an accurate system that optimises processing capacity in an efficient and cost-effective way. Marsh Industries, specialists in off-mains drainage supply, estimates that this processing optimisation can reduce installation costs by as much as 25%, with additional health and safety benefits for installers. The system is perfect for designing off-mains schemes in residential, industrial, education, leisure, amenity and health settings.
A simple linear click and select process guides users through the procedure and the result is a professional presented design, spec and quotation document which includes loadings, drawings, certification and specific design features for the site.
As well as designing exceptionally cost effective and safe off-mains schemes, Marsh’s Gaia Sege systems will comply with the regulatory bodies’ exacting final effluent standards, even for SSSI sites. It uses industry standard data to calculate initial loadings and flows, and peak flows for ammonia, plus total suspended solids (TSS) & biological oxygen demand (BOD) levels. Once the system parameters have been input, Gaia Sege allows users to select the final performance needed on site to reduce tankering and long-term running costs.
The link with Loughborough University remains strong to this day. The two organisations worked together to reassess the currently prescribed testing methods for grease traps and devised a unique test rig and analysis at the University’s centre of excellence.
Marsh’s Grease Management System (GMS) range of grease traps is designed to prevent fats, oil and grease (FOG) build up and, after completing trials, Marsh launched a new range of grease traps which are the only products of their type that have been successfully tested using materials that match the FOG used in the food industry. This pioneering design of grease traps enabled them to win some of the UK’s largest contracts such as supplying Heathrow airport where the brief was to cater for 20,000 meals per day.
Quality and safety standards lie at the heart of the Marsh ethos. All
Marsh sewage treatment plants are certified to the standard EN12566-3 which ensures that final effluent is treated to at least as standard of 20:30:20 and Marsh has the UK rights for the
Polylok Filter, a tertiary treatment filter that further reduces the suspended solids by a further 40%. This is especially desirable in areas of SSSI or for instance sometimes in Scotland where the final effluent has to be treated lower than the standard 20:30:20, due to the surrounding landscapes. By using a Polylok filter in the final zone of the treatment plant this can be achieved.